FuseRing: Redefining Welding for Faster, Safer Joints
A recent demonstration in Brampton, Ontario, highlighted FuseRing’s induction-assisted friction welding, a process that’s catching the attention of industries where precision and safety are paramount, like pipelines and nuclear assembly.
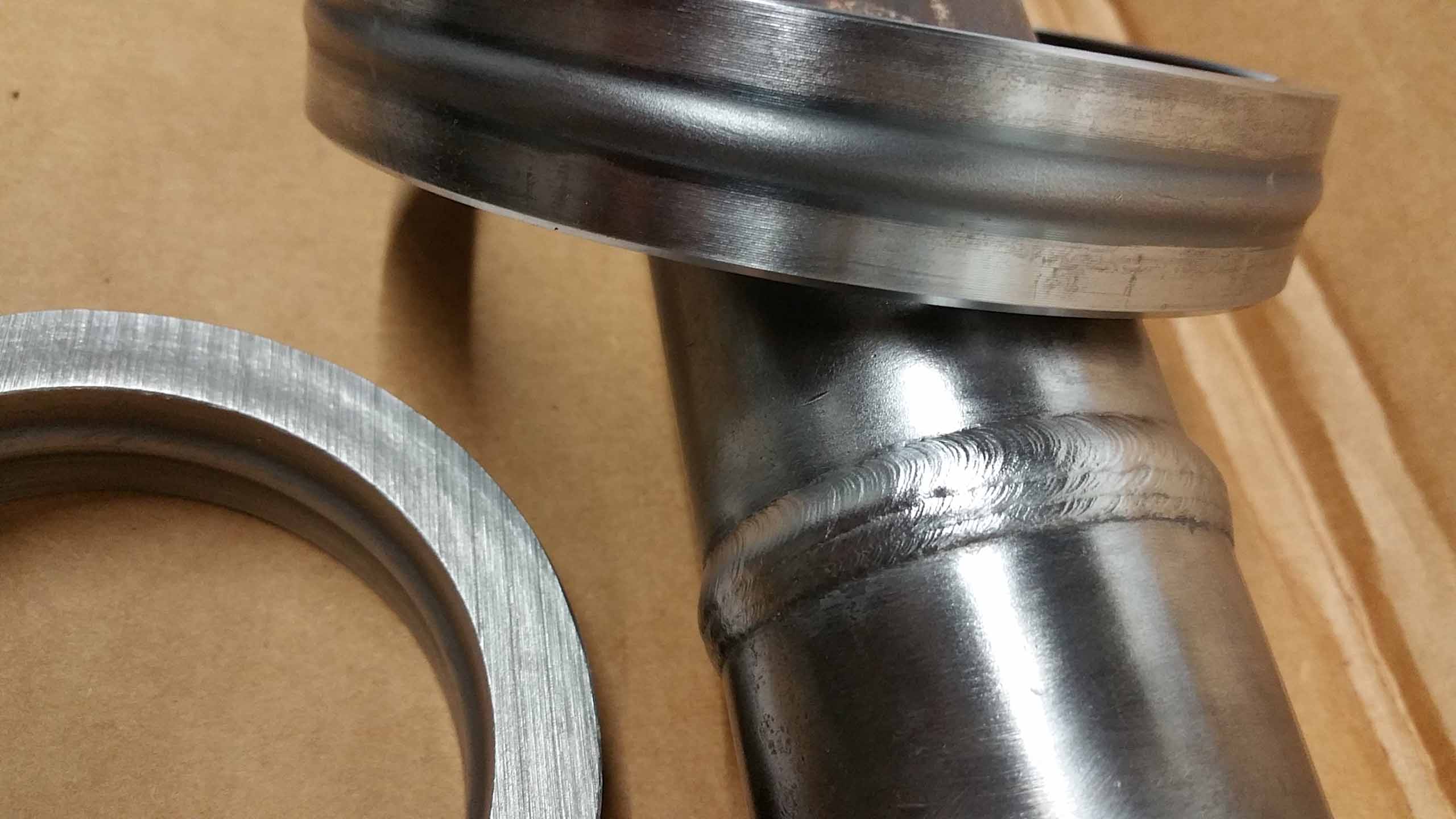
FuseRing’s approach combines induction heating with friction welding principles, creating what inventor David Lingnau calls “spinduction.” The process preheats the ends of two pipes or rods with an induction coil, then applies pressure and rotation for a solid-state fusion that eliminates filler metals and fumes. Impressively, the entire process takes less than 60 seconds, producing joints with high tensile strength and minimal deformation.
Recent demonstrations showcased its application on 4.5-inch carbon steel pipes and zirconium alloy fuel rods—key materials for pipeline and nuclear industries.
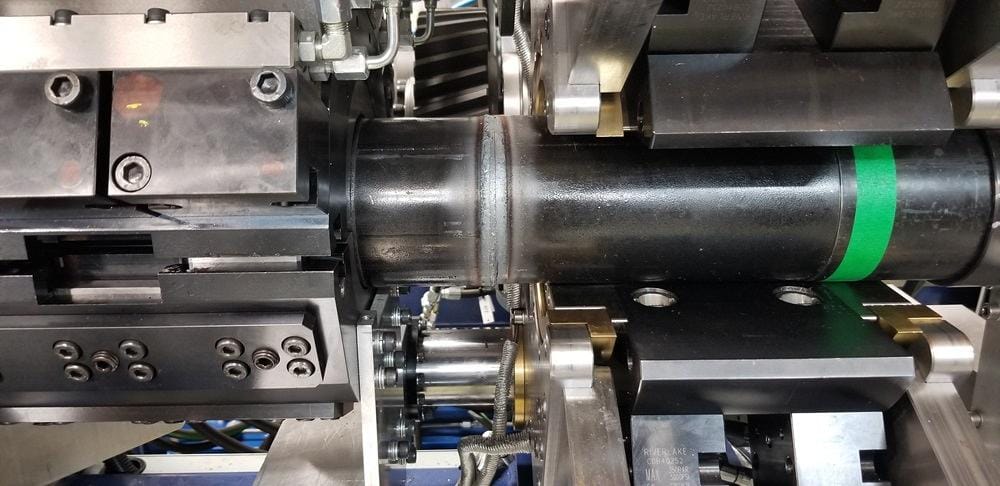
Unlike traditional friction welding, which requires one part to rotate, FuseRing uses a coupler ring to join nonrotatable components. This opens the door for applications in complex assemblies where rotation isn’t feasible. Add the elimination of post-weld processing and minimal heat-affected zones, and you have a solution that seems tailor-made for industries where every second and every degree of heat counts.
Source:
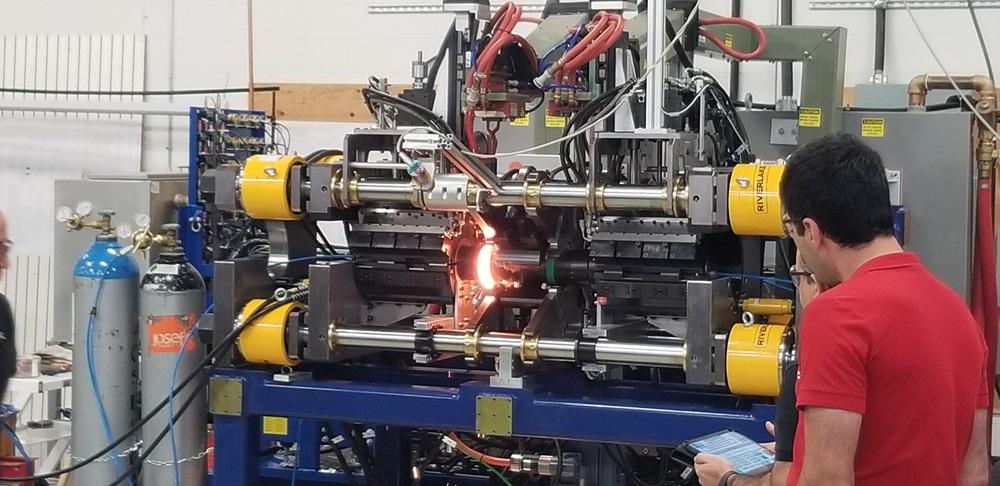
Discussion