Super‑Martensitic Wire Doubles Life of Concast Rollers
UTP's WEARcore 768-S super martensitic flux cored wire claims to improve wear and corrosion resistance, extending continuous‑casting roller life by 2X.
Steel mills have a new option for the most punishing stretch of the continuous‑casting line: UTP’s super‑martensitic WEARcore 768‑S cored welding wire, paired with RECORD SK flux. In qualification runs at Dillinger Hütte, the three‑layer overlay tripled martensite start temperature above ambient, kept delta‑ferrite below 10 %, and delivered a uniform 36 HRC hardness—all while shrugging off mould‑flux‑induced corrosion that normally eats soft martensitic overlays alive.
Field data showed top‑zone rollers hard‑faced with the new wire lasted twice as long as the plant’s conventional martensitic stainless overlay, even under continuous thermal shock at 300–350 °C. Operators reported clean slag release and no dilution issues after the third layer, making the system workable on small 150–300 mm diameters without extra post‑weld heat treatment.
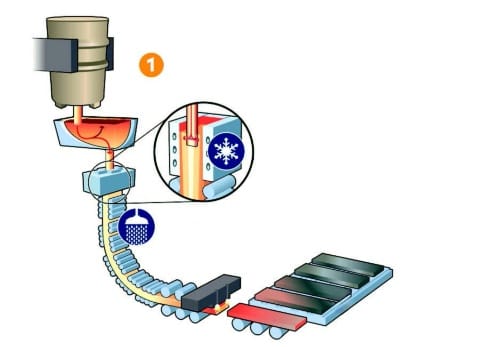
For fabricators, the welding takeaway is straightforward: longer roll life means fewer change‑outs, lower machining hours (the overlay cuts easily with carbide tooling), and a cost curve that bends in the right direction. Super‑martensitic chemistry isn’t new, but packaging it in a stable SAW cored wire for high‑temperature, high‑corrosion service is a notable step forward—and a reminder that smart alloy design can still move the needle on everyday production economics.
Source:
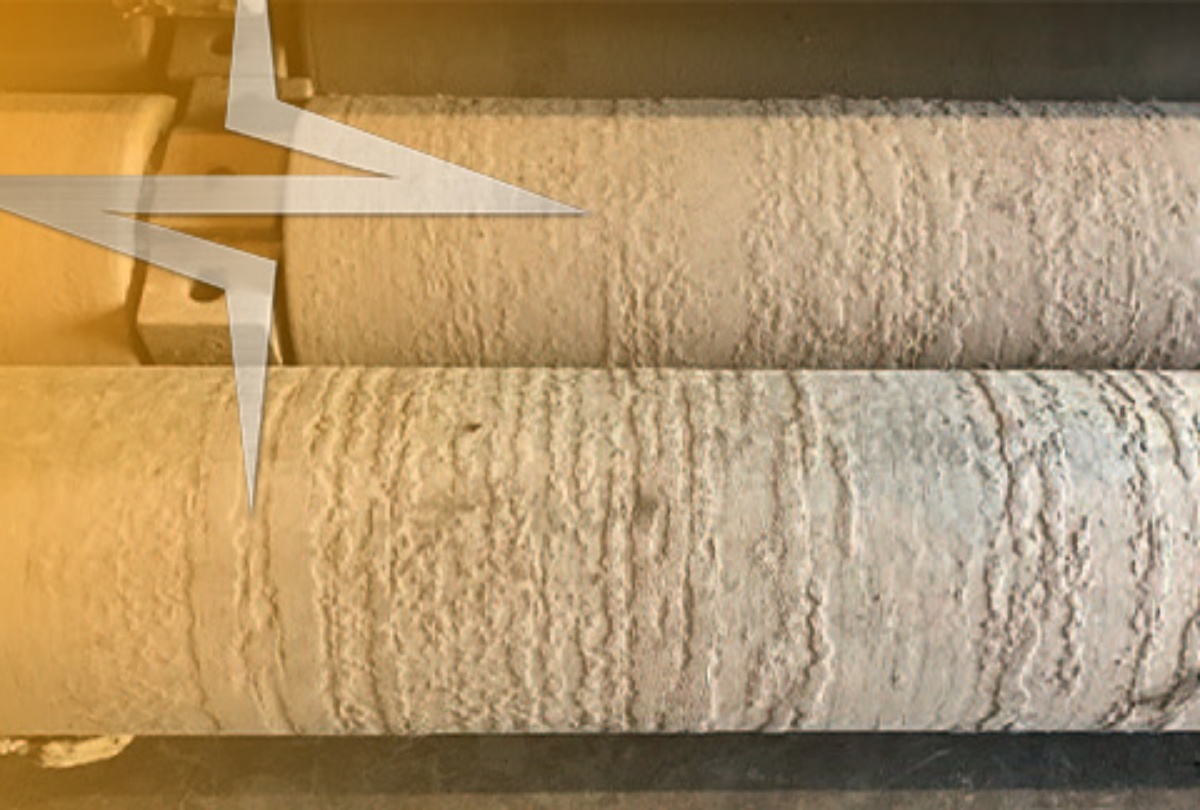
Discussion